Порошковая окрасочная линия SPK для продукции дорожного строительства
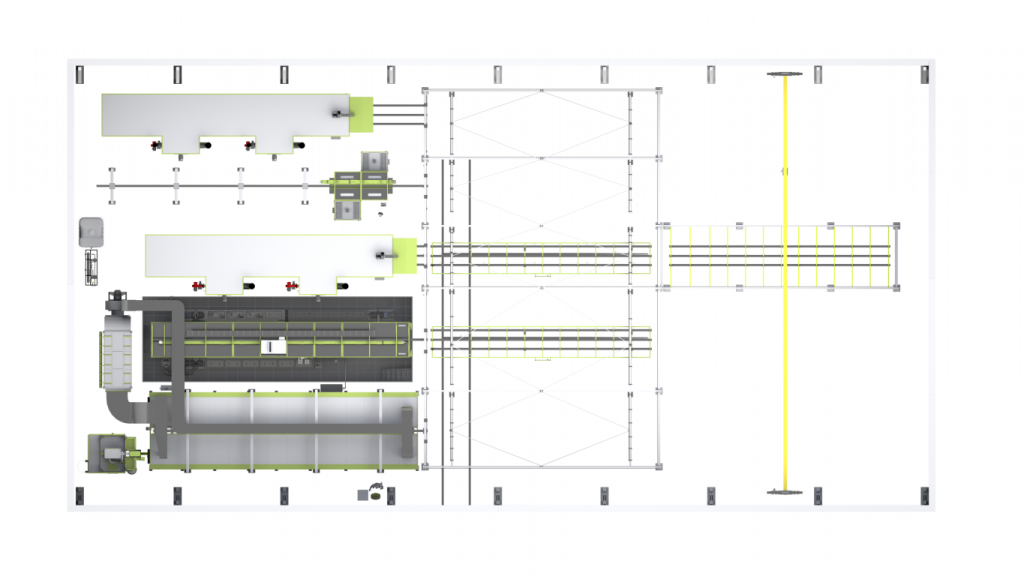
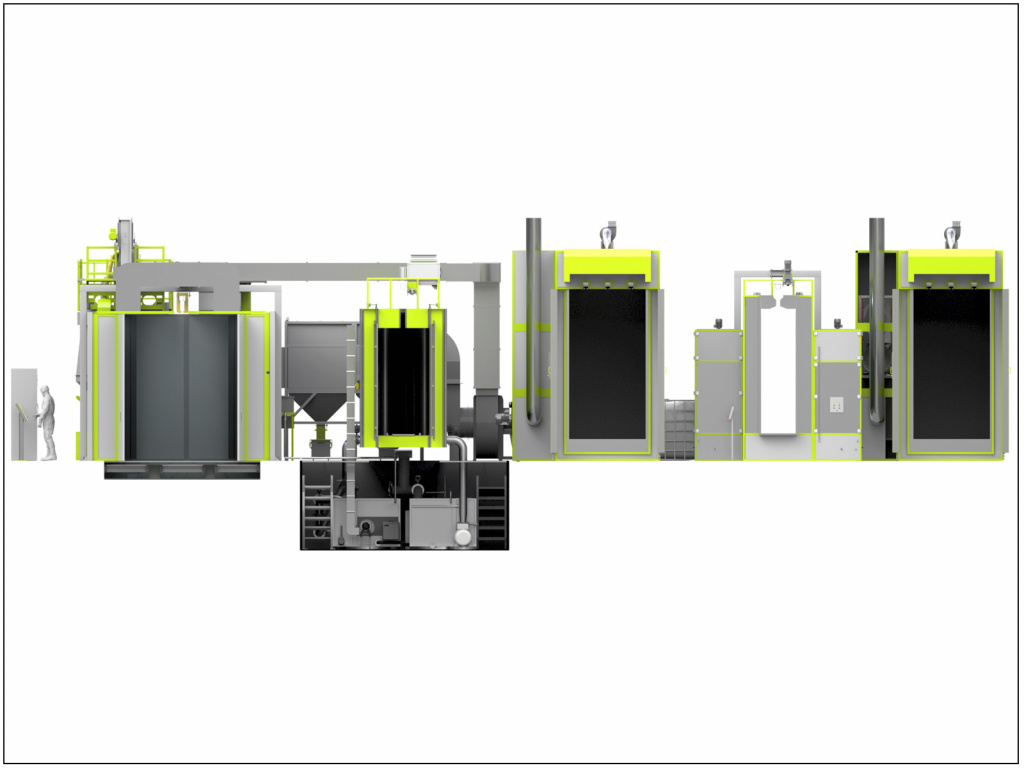
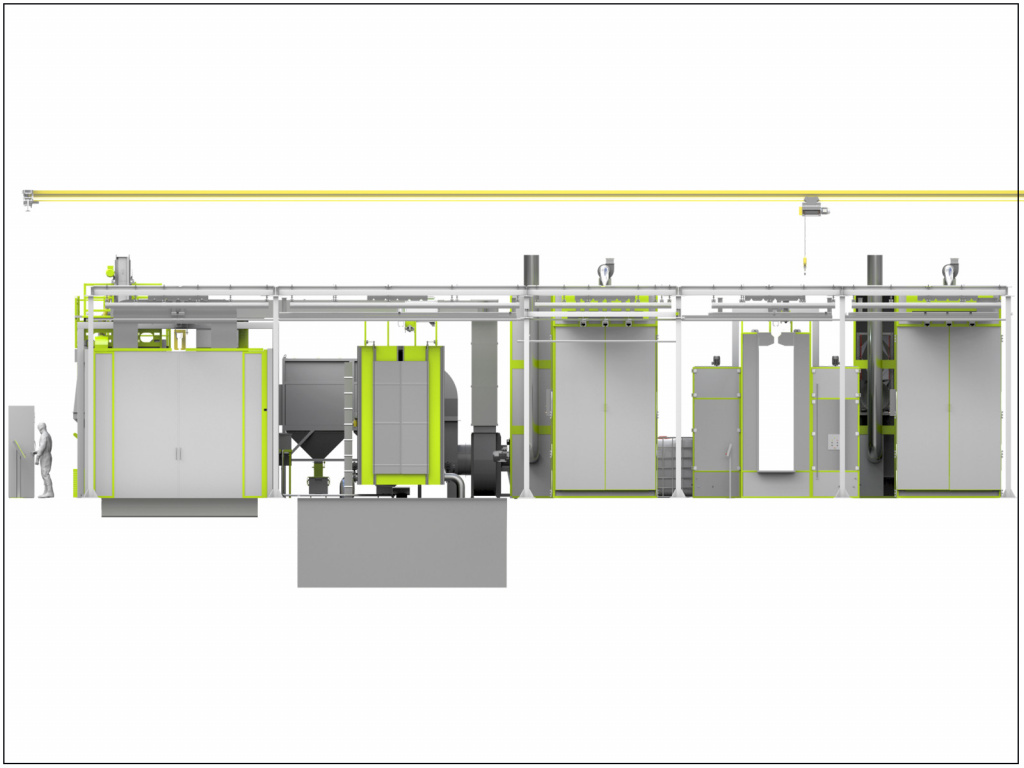
Окрашивание дорожно-строительной техники на линии производителя SPK в составе:
-
Дробеструйной камеры;
-
Камеры обработки поверхности жидкими химическими растворами (SPK-WB-6.2.4)
-
Установки удаления примесей;
-
Сушильной печи;
-
Камеры окрашивания MAX+;
-
Печи отверждения (полимеризации);
-
Транспортной системы (конвейера).
На линии поверхность изделий очищается, промывается, красится порошковыми красками в специальных камерах. На выходе получаем изделие безупречного внешнего вида со стойким к воздействию влаги, перепадам температур покрытием.
Дробеструйная камера
В камере производится зачистка поверхности изделий от механических загрязнений, коррозии, химических пленок. Изделия подаются в камеру подвешенными на рабочий модуль конвейера через распашные ворота (открываются вручную). Внутренняя поверхность камеры защищена резиновым покрытием. Работают два оператора–дробеструйщика. Очистка производится металлической дробью (колотой, стальной, стеклянной). Для операторов предусмотрены две сервисные двери 800х2000 мм. В камере установлена ВФУ замкнутого типа. Установлена система рекуперации дроби для экономии расходных материалов.
Камера обработки поверхности жидкими химическими растворами
В камере поверхность изделий промывается жидкими химическими растворами, водой с целью обезжиривания/фосфатирования. Жидкости подогреваются до t° 40—60 °C, используется система рециркуляции для экономии растворов. Система автоматизированного контроля и расхода химических веществ. Очистная система для удаления шлама и масел. Фильтры-каплеуловители в ВФУ.
Установки удаления примесей
Удаление из воды примесей размером 0,001–0,0001 микрон за счет обратного осмоса.
Сушильная печь
В сушильной печи влага на поверхности изделий высыхает при t° 110—160 °C. Режим и время сушки устанавливаются оператором вручную.
Камера окрашивания MAX+
В камере на изделия наносится порошковая краска. Установлена система рекуперации для сбора и возврата в красящее устройство не осевшей краски. ВФУ обеспечивает класс очистки воздуха F8. Постоянный расход воздуха обеспечивается за счет частотных преобразователей и контроля давления в системе при работе вентилятора. Установлена автоматизированная система контроля состояния фильтров, устройств-потребителей сжатого воздуха. Все данные отражаются на централизованной панели управления.
Печь отверждения (полимеризации)
В печи отверждения формируется покрытие на поверхности изделий за счет процесса полимеризации (выдерживании изделия в печи при t° 140—200°C). Режим и время полимеризации устанавливаются оператором вручную. Побочные продукты процесса полимеризации удаляются через вытяжной зонт. Использование комплекса фальш покрытий пола, потолка, регулируемой плавной работы газовой горелки, частотно-управляемого вентилятора ВФУ позволяет получить качественное декоративно-защитное покрытие.
Транспортная система (конвейер)
Изделия по этапам технологического процесса перемещаются на рабочих модулях подвесной транспортной системы без перевешивания изделий между камерами и без потери заземления. При продольном перемещении используется ручной режим. Рабочие модули системы собраны на специальных каретках с возможностью поперечного перемещения, накапливания в зонах между камерами для остывания. Внутри камер рабочие модули передвигаются с помощью устройств качения, протяжек в автоматическом (полуавтоматическом режиме).
Операции, выполняемые в линии
-
помещение изделия на рабочий модуль конвейера;
-
дробеструйная очистка;
-
обезжиривание/фосфатирование, выдержка для стекания раствора, промывка технической водой, промывка деминерализованной водой, выдержка для стекания жидкости;
-
удаление остатков влаги (сушка поверхности);
-
остывание изделия;
-
нанесение порошкового состава;
-
полимеризация порошковой краски;
-
остывание изделия;
-
удаление изделия с рабочего модуля конвейера.