Порошковая окраска металлических изделий: технология и оборудование
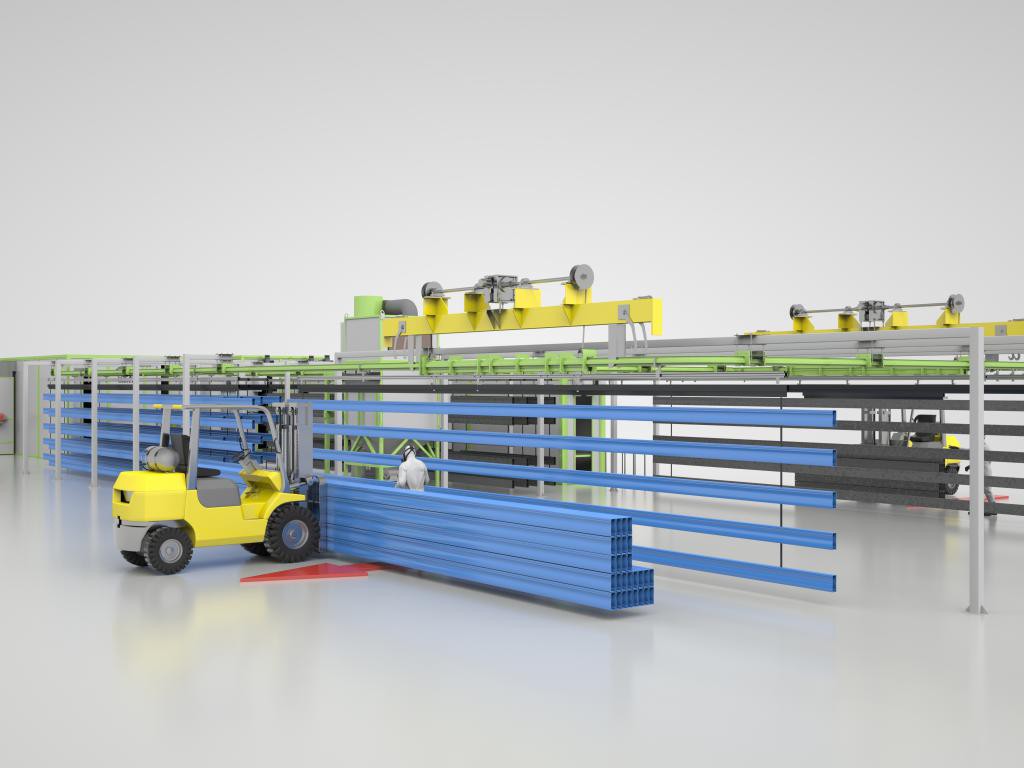
Порошковая окраска металлических изделий – передовая технология, обеспечивающая долговечность и высокую стойкость покрытия к внешним воздействиям. Этот метод используется в различных отраслях промышленности, от автомобильной до строительной, благодаря своим многочисленным преимуществам: экологичности, экономичности и возможности получения высококачественного покрытия. Порошковая окраска включает несколько ключевых этапов, таких как подготовка поверхности, нанесение грунта, нанесение порошковой краски и полимеризация, каждый из которых требует специализированного оборудования и строгого соблюдения технологического процесса.
Технология порошковой окраски
Технология порошковой окраски металлов включает в себя нескольких важных этапов:
- Подготовка поверхности. Этот этап включает обезжиривание, фосфатирование и сушку. Для этого применяются дробеструйные камеры и агрегаты химической подготовки поверхности с ручной или автоматической обработкой. Используются также специальные печи для сушки.
- Нанесение грунта. Специальные агрегаты наносят грунт, что повышает адгезию краски и защищает металл от коррозии.
- Нанесение порошковой краски. Применяются окрасочные кабины (обитаемые и необитаемые) с циклонными и картриджными системами фильтрации. Используются ручные системы электростатического нанесения и роботизированные системы.
- Полимеризация. Процесс происходит в печах (электрических, газовых и дизельных), а также в инфракрасных камерах. Температура полимеризации регулируется в пределах 160-210°C.
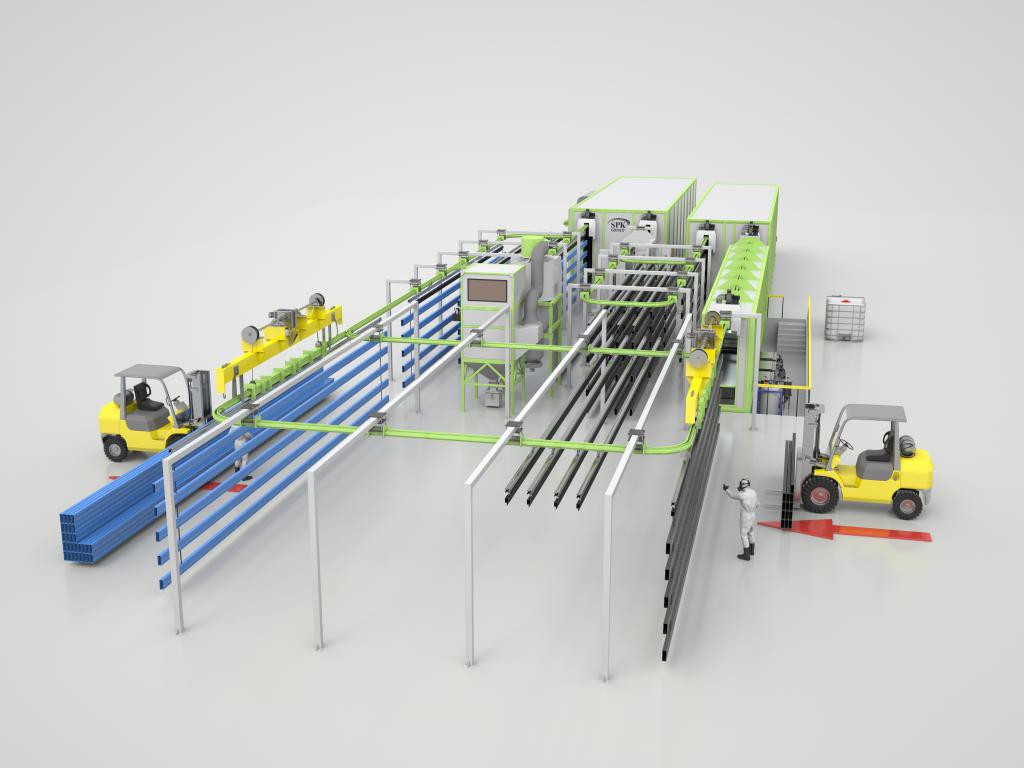
Каждый этап требует строгого соблюдения технологических норм и использования надежного оборудования, что обеспечивает высокое качество покрытия и долговечность изделий.
Оборудование для подготовки поверхности
Для качественной линии окраски металлоконструкций критически важна правильная подготовка поверхности. Дробеструйные камеры используются для очистки металла от окалины, ржавчины и других загрязнений. Эти камеры оснащены системой рекуперации дроби, что позволяет повторно использовать абразивные частицы, улучшая эффективность и снижая затраты. Дробеметные установки автоматизируют процесс, обеспечивая равномерное распределение абразива и высокую производительность.
Агрегаты химической подготовки поверхности предназначены для обезжиривания и фосфатирования. Они могут быть с ручной или автоматической обработкой, что позволяет адаптироваться под различные объемы производства. Температура растворов регулируется в диапазоне 40-65°C для оптимального обезжиривания и нанесения фосфатного слоя. Использование автоматических систем дозирования и контроля параметров обеспечивает стабильность процесса.
Печи сушки используются для удаления влаги с поверхности изделий перед нанесением порошковой краски. Температура в печах регулируется в пределах 110-160°C, что обеспечивает эффективную сушку без перегрева изделий. Время цикла сушки после выхода на режим устанавливается оператором вручную, что позволяет адаптироваться к различным типам продукции и требованиям заказчиков.
Нанесение грунта
Нанесение грунта – ключевой этап в процессе порошковой окраски. Грунт обеспечивает адгезию порошковой краски к металлу и защищает изделие от коррозии. В линии порошковой окраски металлоизделий используется несколько типов агрегатов для нанесения грунта.
Агрегаты катафорезного покрытия
Этот метод обеспечивает равномерное нанесение грунта даже на сложные формы изделий. Основан на электроосаждении грунта на поверхности изделия. Изделие погружается в ванну с грунтовочным раствором, к которому подается электрический ток. Это обеспечивает равномерное нанесение грунта даже на сложные формы изделий и внутренние полости. Катафорезный метод используется для изделий, требующих высокой коррозионной стойкости и долговечности покрытия.
Агрегаты анафорезного покрытия
Подходят для изделий с высокой степенью коррозионной устойчивости. Подобно катафорезному покрытию, анафорезный метод также использует электрический ток для нанесения грунта. Однако в этом случае заряд противоположен. Этот метод подходит для изделий, требующих средней степени коррозионной устойчивости. Анафорезное покрытие обеспечивает равномерное и качественное нанесение грунта на поверхности изделий, что критически важно для последующего нанесения порошковой краски.
Агрегаты для нанесения жидкого грунта
Применяются для создания начального защитного слоя перед нанесением порошковой краски. Жидкий грунт наносится с помощью распылителей, что позволяет получить равномерное покрытие. Агрегаты для жидкого грунтования могут быть автоматическими или ручными, что позволяет адаптироваться под различные объемы и типы изделий.
Использование различных типов оборудования позволяет адаптироваться к специфическим требованиям каждого изделия и обеспечивает надежную защиту от коррозии.
Нанесение порошковой краски
Нанесение порошковой краски – ключевой этап на линии порошковой окраски металлоизделий. Этот процесс начинается с размещения изделий в специальных окрасочных кабинах. Применяются как обитаемые, так и необитаемые кабины, оснащенные циклонными и картриджными системами фильтрации, которые обеспечивают чистоту и эффективность процесса.
Окрасочные кабины оснащены ручными системами электростатического нанесения, а также системами на основе двух- и трехосевых манипуляторов и роботизированными системами. Это позволяет наносить краску равномерно и точно на всю поверхность изделий, включая сложные геометрические формы.
Процесс нанесения краски контролируется через централизованные панели управления, что обеспечивает стабильность и качество покрытия. Средняя скорость нанесения краски составляет 4 м/мин, что позволяет обработать большое количество изделий за короткий период времени. Рекуперационные системы обеспечивают возврат до 96% излишков краски, что делает процесс экономичным и экологически безопасным.
Полимеризация
Полимеризация – завершающий этап в технологии порошковой окраски металлов. Этот процесс проходит в специальных печах полимеризации, которые могут быть электрическими, газовыми или дизельными, а также инфракрасными (ИК). Температура в печах регулируется в диапазоне от 160 до 210°C, что обеспечивает равномерное расплавление и затвердевание порошковой краски на поверхности изделий.
Печи полимеризации оснащены фальшполом и фальшпотолком для равномерного распределения температуры. Время полимеризации варьируется от 10 до 30 минут в зависимости от типа изделия и толщины покрытия. Процесс контролируется операторами с помощью панелей управления, что позволяет точно задавать параметры температуры и времени. Вентиляционные системы с частотным управлением обеспечивают удаление продуктов полимеризации, поддерживая чистоту и безопасность в производственном помещении.
Процесс полимеризации включает несколько шагов:
- Загрузка изделий в печь. Изделия, покрытые порошковой краской, помещаются в печь полимеризации. Размещение должно обеспечивать равномерный доступ тепла ко всем частям изделия.
- Регулировка температуры. Температура внутри печи настраивается в пределах 160-210°C в зависимости от типа изделия и состава краски. Точная настройка важна для достижения оптимального результата.
- Нагрев и плавление. При достижении необходимой температуры порошковая краска начинает плавиться, равномерно распределяясь по поверхности изделия.
- Полимеризация. Краска затвердевает, образуя прочное и стойкое покрытие. Этот этап длится от 10 до 30 минут. Время зависит от типа изделия и толщины покрытия.
- Контроль процесса. Операторы с помощью панелей управления следят за температурой и временем полимеризации. Автоматические системы управления обеспечивают стабильные условия и предотвращают перегрев.
- Удаление продуктов полимеризации. Вентиляционные системы с частотным управлением удаляют испарения и продукты разложения, поддерживая чистоту и безопасность в печи.
- Охлаждение изделий. После завершения полимеризации изделия охлаждаются до комнатной температуры, что позволяет краске окончательно затвердеть.
- Выгрузка изделий. Охлажденные и полностью полимеризованные изделия вынимаются из печи, готовые к дальнейшей обработке или использованию.
Этот пошаговый процесс обеспечивает высокое качество и долговечность покрытия, что делает порошковую окраску одним из наиболее востребованных методов обработки металлических изделий.
Транспортные системы
В линии порошковой окраски металлоизделий важную роль играют транспортные системы. Они обеспечивают перемещение изделий между различными этапами технологического процесса, поддерживая высокую производительность и качество окраски.
Существует несколько типов транспортных систем:
- Монорельсовые ручные конвейеры. Используются для небольших производств и обеспечивают гибкость перемещения изделий.
- Автоматические цепные конвейеры. Позволяют автоматизировать процесс, увеличивая скорость и эффективность производства.
- Системы Power&Free. Обеспечивают высокую гибкость и позволяют накапливать изделия на разных этапах процесса.
Эти транспортные системы могут работать со скоростью до 8 м/мин, обеспечивая точное позиционирование и перемещение изделий весом до 120 кг. Автоматизированные системы управления контролируют все этапы процесса, включая скорость перемещения, распределение нагрузки и обеспечение безопасности.
Системы управления и вспомогательное оборудование
Для эффективного функционирования окрасочной линии необходимы современные системы управления и вспомогательное оборудование. Эти системы играют ключевую роль в обеспечении стабильности и качества производственного процесса. Контролируют каждый этап технологического процесса, от подготовки поверхности до полимеризации. Централизованные панели управления обеспечивают мониторинг и регулирование параметров температуры, времени и скорости конвейеров. Важно поддерживать оптимальные концентрации химических растворов и автоматически обновлять их. Современные панели управления позволяют операторам следить за всеми ключевыми параметрами, обеспечивая точность и своевременное вмешательство при необходимости.
Вспомогательное оборудование включает различные системы, необходимые для поддержания и улучшения качества покрытия:
- Системы очистки воды и воздуха. Обеспечивают удаление загрязнений и поддержание чистоты в производственном процессе. Системы очистки воды включают установки деминерализации и локальные очистные сооружения, которые удаляют из воды соли жесткости, сульфаты, нитраты и другие примеси. Системы очистки воздуха оснащены фильтрами для удаления пыли и частиц краски.
- Лабораторное оборудование. Используется для контроля качества покрытий. Это включает оборудование для тестирования адгезии, твердости и стойкости покрытия к коррозии.
- Подвески и маскирующие элементы. Подвески обеспечивают надежное закрепление изделий на конвейере, а маскирующие элементы защищают определенные участки изделия от покрытия, что важно для точного нанесения краски.
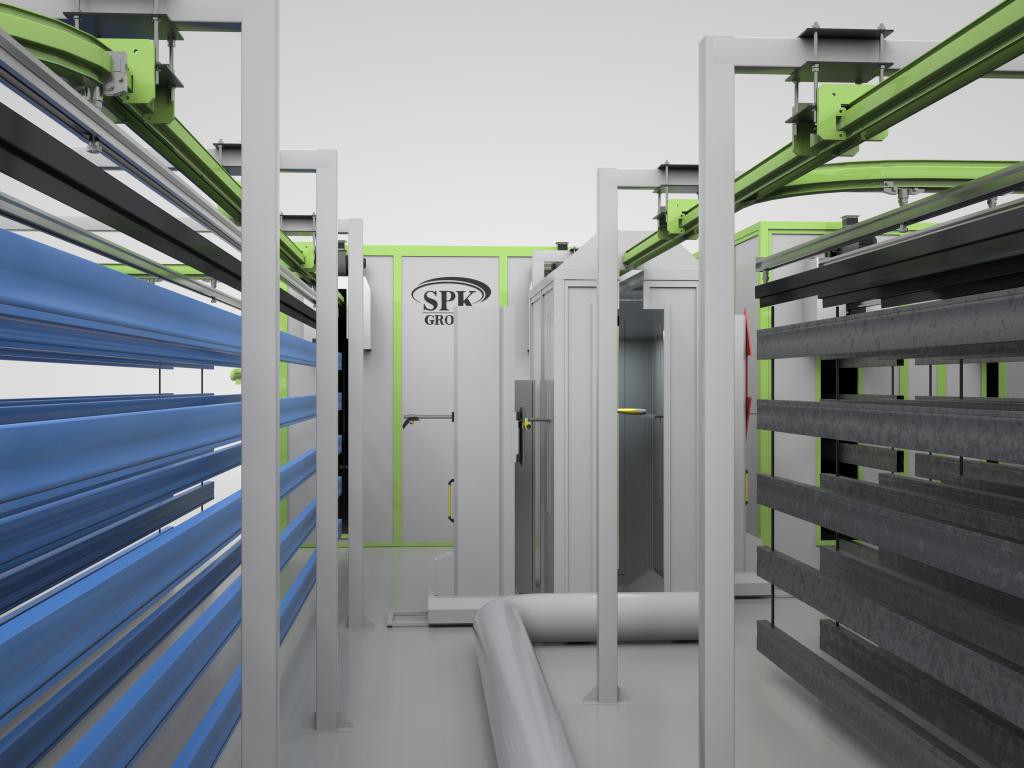
Современные решения в области управления и вспомогательного оборудования позволяют значительно повысить производительность и качество порошковой окраски.
Контроль качества в процессе порошковой окраски
Контроль качества является неотъемлемой частью процесса порошковой окраски металлических изделий. Он охватывает все этапы производственного цикла и направлен на обеспечение высокого уровня соответствия продукции установленным стандартам. Эффективный контроль качества включает несколько ключевых аспектов: проверку качества поверхности, тестирование адгезии, оценку толщины и твердости покрытия, а также испытания на устойчивость к коррозии и механическим повреждениям.
Визуальный осмотр и проверка качества поверхности
Начальный этап контроля качества начинается с визуального осмотра поверхности металла после подготовки. Важно убедиться, что поверхность полностью очищена от окалины, ржавчины, жировых и других загрязнений. Любые недостатки на этой стадии могут негативно сказаться на адгезии грунта и порошковой краски. Для более точной проверки используются специальные инструменты, такие как профилометры, которые измеряют шероховатость поверхности и позволяют оценить готовность изделия к следующему этапу.
Тестирование адгезии
Одним из важнейших показателей качества покрытия является адгезия – сила сцепления краски с поверхностью металла. Для проверки адгезии используют несколько методов, включая тест среза и тест решетки. В тесте среза на покрытии делают надрезы в форме крестов, затем с помощью клейкой ленты проверяют, насколько краска удерживается на поверхности. Тест решетки включает нанесение сетки надрезов и оценку отслоения краски. Высокая адгезия свидетельствует о качественном нанесении грунта и краски, а также о правильной подготовке поверхности.
Измерение толщины покрытия
Толщина покрытия – еще один важный параметр, который необходимо контролировать. Измерение толщины проводится с помощью магнитных и вихретоковых толщиномеров. Эти устройства позволяют точно определить толщину нанесенного слоя порошковой краски, что критично для обеспечения долговечности и защитных свойств покрытия. Оптимальная толщина варьируется в зависимости от типа изделия и условий его эксплуатации, но обычно составляет от 60 до 120 микрон.
Оценка твердости покрытия
Твердость покрытия напрямую влияет на его устойчивость к механическим повреждениям. Для оценки твердости применяются тесты с использованием карандашей различной твердости (тест карандашом) или ударные испытания. Тест карандашом заключается в проведении карандашом с определенной твердостью по поверхности покрытия. Результаты позволяют определить устойчивость покрытия к царапинам и повреждениям. Ударные испытания включают падение груза на покрытие с определенной высоты, что позволяет оценить его устойчивость к ударным нагрузкам.
Испытания на коррозионную стойкость
Коррозионная стойкость является одним из ключевых факторов, определяющих долговечность покрытий. Для ее оценки используются различные методы, включая испытания в соляном тумане и ускоренные атмосферные испытания. В испытаниях в соляном тумане образцы покрытий подвергаются воздействию аэрозоля из раствора соли, что имитирует коррозионные условия. Результаты этих тестов позволяют судить о способности покрытия защищать металл от коррозии в агрессивных средах.
Механические испытания
Кроме коррозионной стойкости, важно оценить механическую прочность покрытия. Для этого проводят тесты на изгиб и ударопрочность. Испытания на изгиб включают сгибание покрытых металлических пластин под различными углами для оценки эластичности покрытия. Ударопрочность проверяется путем нанесения ударов различной силы и оценки повреждений. Эти тесты позволяют определить, насколько хорошо покрытие выдерживает механические нагрузки и деформации.
Порошковая окраска металлических изделий - это передовая технология, обеспечивающая высококачественное, долговечное и стойкое к внешним воздействиям покрытие. Этот метод широко применяется в промышленности благодаря своей экологичности и экономичности. Строгое соблюдение всех этапов технологического процесса и использование специализированных окрасочных линий является залогом успешного применения данной технологии.